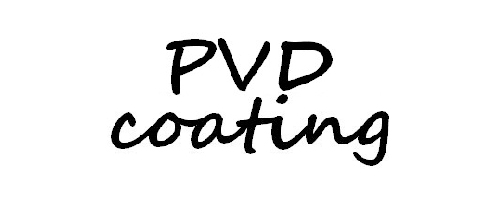
PVD coating, známý také jako PVD povlakování, je povrchová úprava (coat = kabát), která může být aplikována na povrchy různých výrobků. Primárním účelem je zvýšení odolnosti a prodloužení trvanlivosti produktu. Zkratka PVD pochází z anglického označení Physical Vapor Deposition. V češtině se používá označení Fyzikální depozice z plynné fáze.
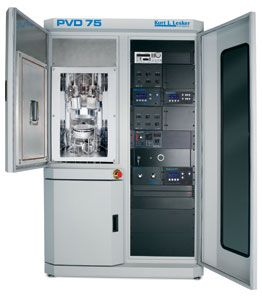
Jak je úprava prováděna?
Zjednodušeně řečeno se jedná o proces nanášení povrchového materiálu ve velmi tenké vrstvě. Existuje několik metod provádění PVD. Napařování ve vakuu při teplotách mezi 150 °C a 500 °C ve speciální iontové komoře. Uvolněné částice materiálu pro PVD jsou ionizovány a reagují s atmosférou uvnitř komory, složenou z inertního plynu (zpravidla Argonu) a reaktivního plynu (zpravidla Dusíku). Následně se usazují na povrchu ošetřovaného předmětu, kde vytvoří tenký, souvislý a vysoce přilnavý povlak. Mezi jiné technologické postupy se stejným dosaženým výsledkem patří naprašování, depozice elektronovým svazkem a pulsní laserová depozice. Aby se dosáhlo rovnoměrné tloušťky vrstvy, ošetřované předměty se otáčejí rovnoměrnou rychlostí kolem několika os.
Nejčastěji užívaný PVD coating
Mezi nejčastěji používané PVD povlakování patří Titanium coating – Tin. Existuje také několik dalších komerčně používaných variant TiN, které byly vyvinuty v posledních deseti letech. Je to Titanium carbon nitrid – TiN s uhlíkem, TiCN, dále Titanium aluminium nitrid – TiN s hliníkem, TiAlN nebo AlTiN a také kombinace hliníku i uhlíku. Mezi další rozšířené PVD povrchové úpravy patří CrN coating (na bázi nitridu chromu), ZrN coating (na bázi Zirconium nitridu) nebo Alpha™ coating – Tin + ZrN.
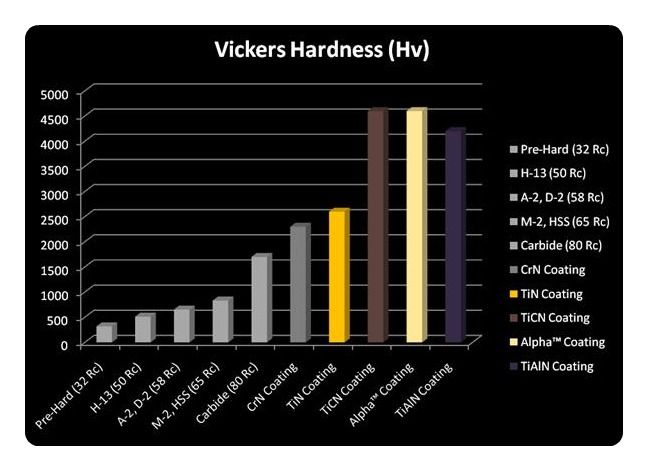
Výsledek úprav PVD coating
Přínosem povrchových úprav PVD je značné zlepšení vlastností ošetřeného produktu, jako jsou nízké tření, vysoká tvrdost, odolnost vůči oděru i vůči vysoké teplotě, odolnost vůči korozi i vůči kyselinám.
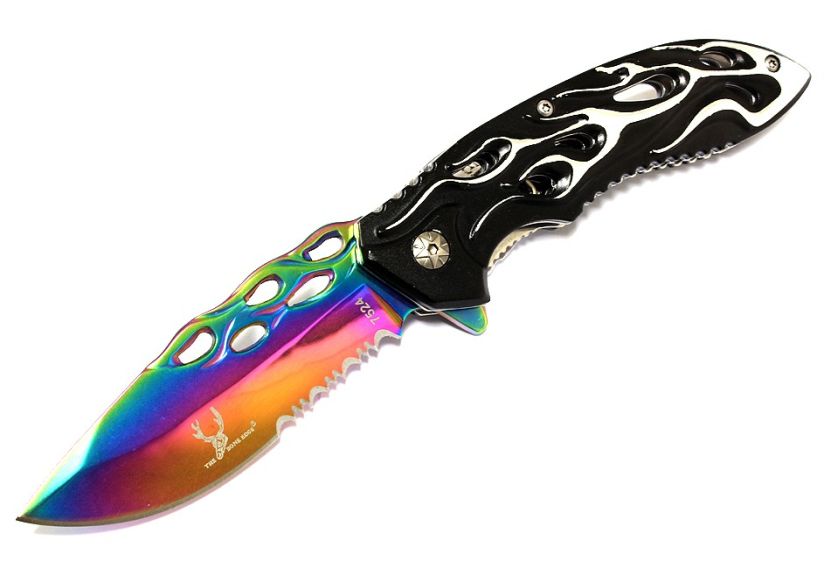